Dutch designers Suzanne Oude Hengel and Joris de Groot have developed a shoe using just one material – a recyclable thermoplastic that can be knitted, 3D-printed and welded.
Welded Loop is a research-led project exploring how thermoplastic polyurethane (TPU) can be used to create every component in a pair of sneaker-style shoes.
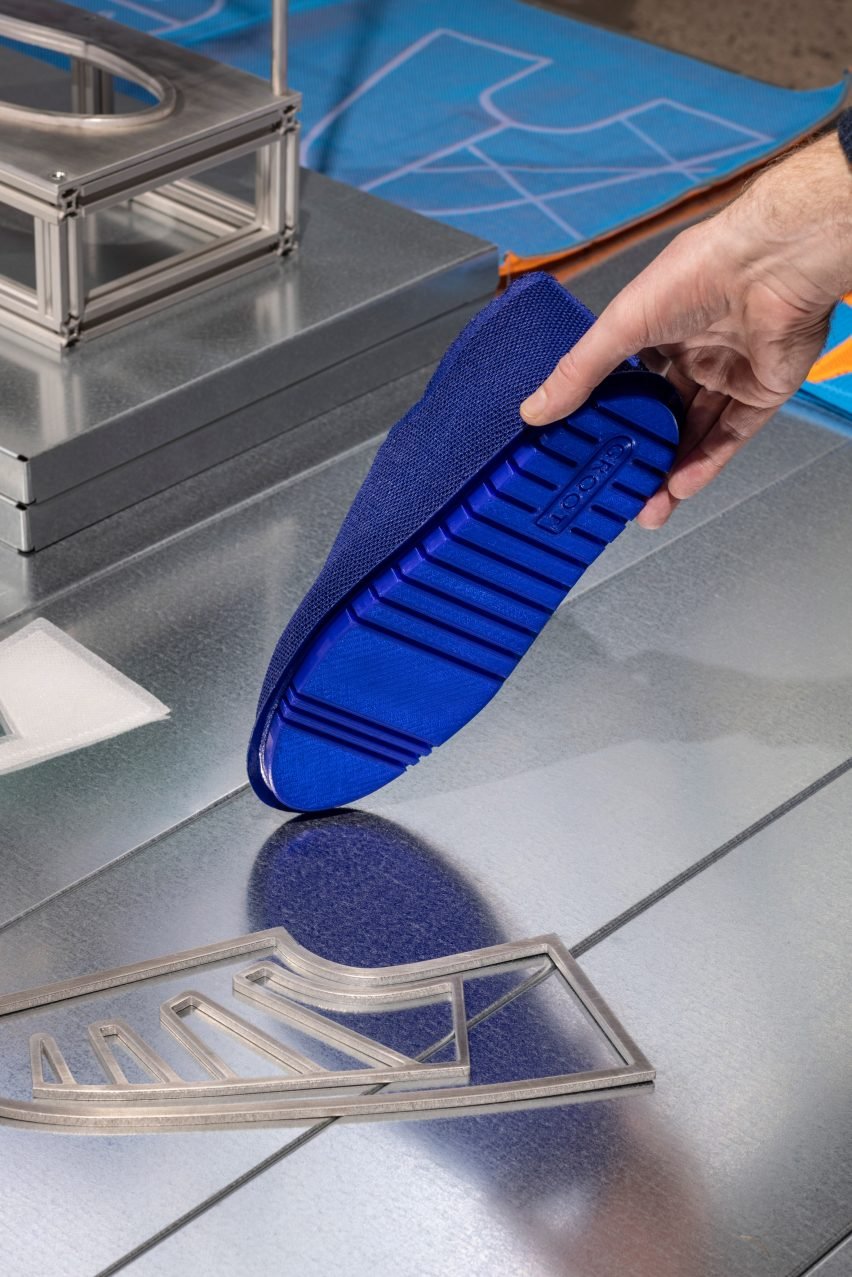
The designers have created a prototype for mono-material footwear that combines knitted TPU uppers with 3D-printed TPU soles and details. Parts are welded together, removing the need for glues or other material components.
The project brings together the knitting expertise of Oude Hengel, founder of textile design studio Knit in Motion, and de Groot’s knowledge of high-frequency welding, a highly efficient and precise method of joining plastic parts.
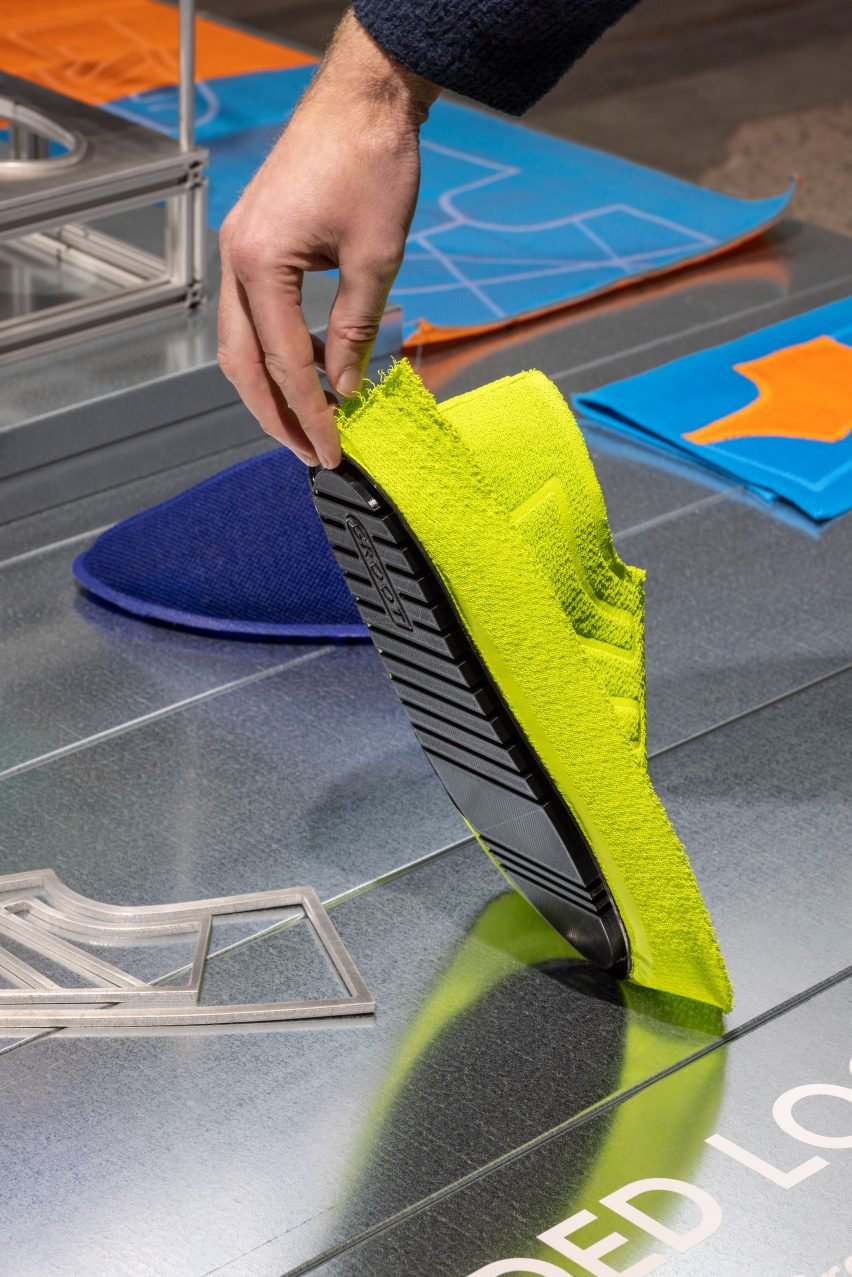
While most shoes are difficult to recycle, due to the mix of different components and glues, Welded Loop offers a potentially more sustainable alternative.
“There is a lot of functionality to answer to in shoes, which is why you normally see so many different materials and glues,” Oude Hengel told Dezeen.
“Our challenge was to make a very clear and simple shoe using a single material,” added de Groot.
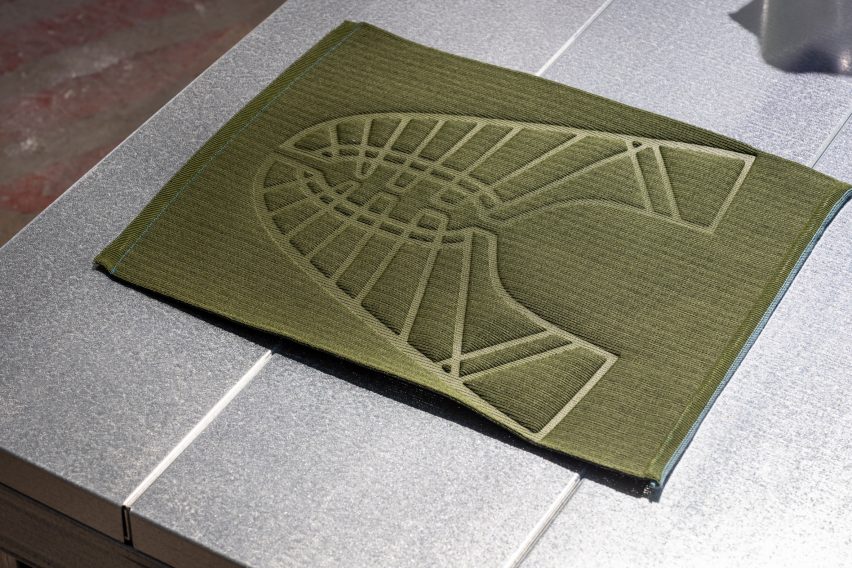
The process, he explained, involves very few processes.
They start by knitting a templated textile using TPU yarns, onto which they weld 3D-printed eyelets. They thermoform this around a mould to create the upper, then weld it to the 3D-printed soles.
“In three welds, you have a whole shoe with a lot of details – it’s not a boring shoe,” said de Groot.
The two designers have known each other for over a decade and collaborated on other projects in the past. They came up with the idea for Welded Loop after discovering it was possible to source yarns that are 100 per cent TPU.
De Groot was already familiar with TPU, having previously worked on designs for waterproof clothing and accessories. These products typically use composite yarns that are coated with TPU, resulting in less versatile textiles.
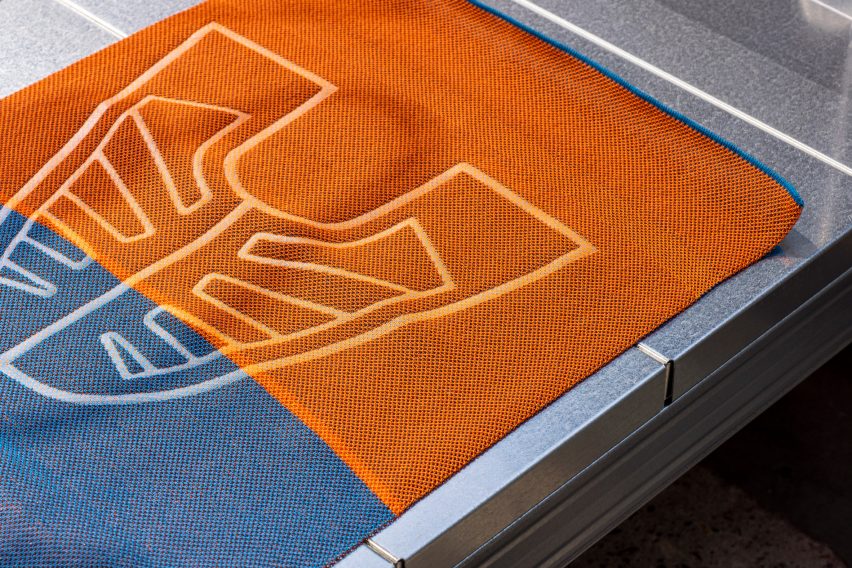
He and Oude Hengel became interested in the different properties a knitted version of TPU might offer.
“In rain gear, it’s always closed to both water and air,” de Groot said. “But if you have an open structure, it creates possibilities to make all new kinds of products.”
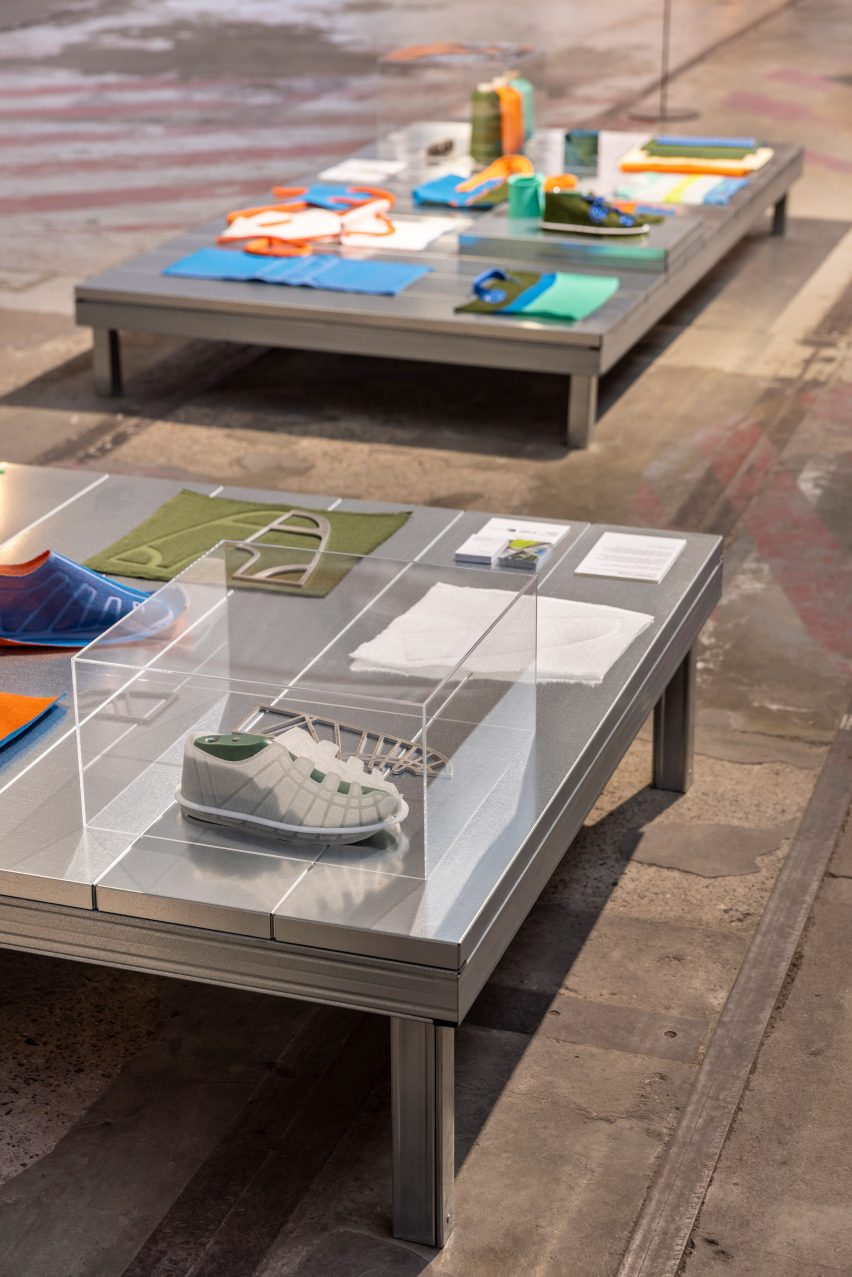
So far, the project is self-initiated. The designers received some funding from the Experiment Grant Scheme, financed by Creative Industries Fund NL, which Oude Hengel said covered the cost of the materials.
They presented the results of the first three months of research in Eindhoven during Dutch Design Week, as part of the Something Bigger exhibition at Schellens Fabriek.
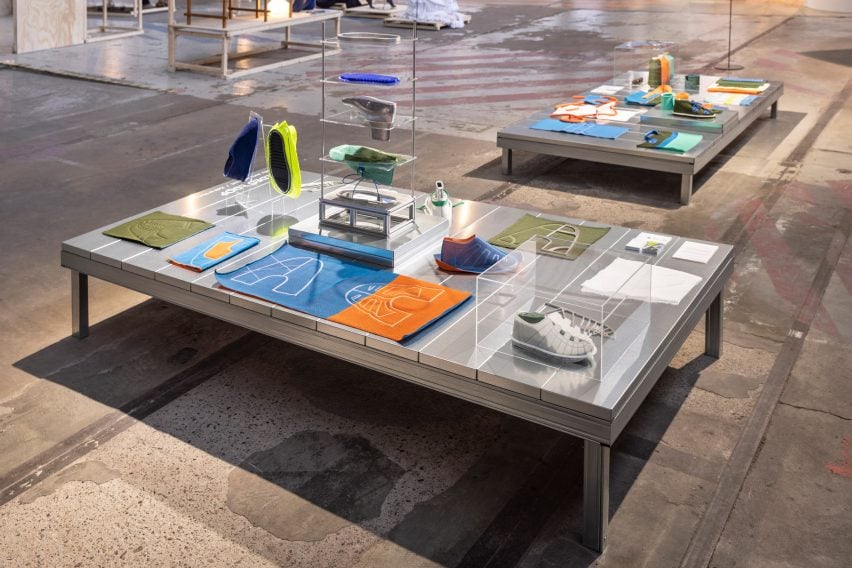
This is just the start, according to Oude Hengel and de Groot. They plan to continue experimenting with different ways of using TPU yarn to create mono-material products.
They believe the shoes could have a market that goes beyond their sustainability potential.
“The aesthetic is born out of the making, so it’s a different aesthetic to typical shoes,” said de Groot.
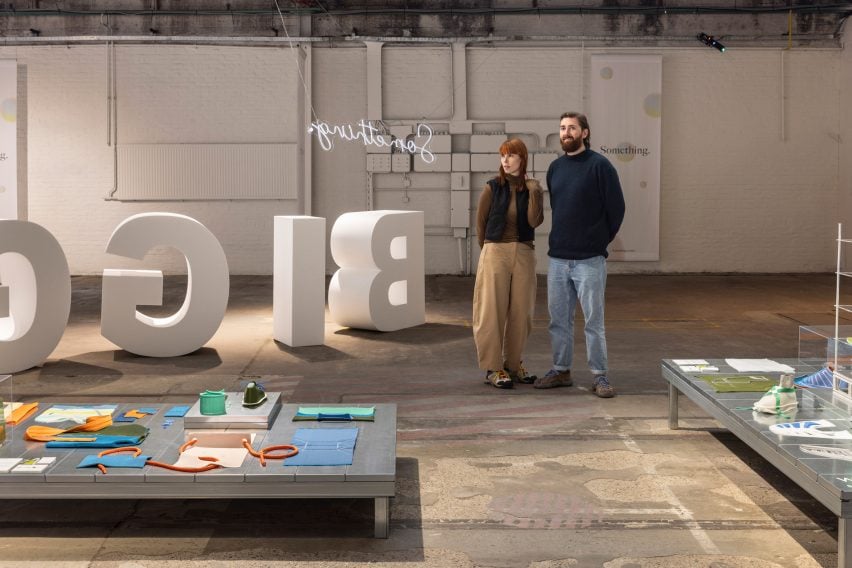
In the long term, the designers hope to find a commercial partner to help them turn the Welded Loop concept into reality. But for now, they plan to continue exploring for themselves.
“There is so much potential that we haven’t researched yet,” said Oude Hengel. “We want to explore the full scope of what’s possible before we become too led by creating a product.”
Other shoe brands that have created mono-material trainers include Vivobarefoot, which recently developed a prototype trainer that is 3D-printed from compostable materials, while Adidas made 1,500 prototypes of a trainer also entirely made from thermoplastic polyurethane and assembled using heat rather than glue.